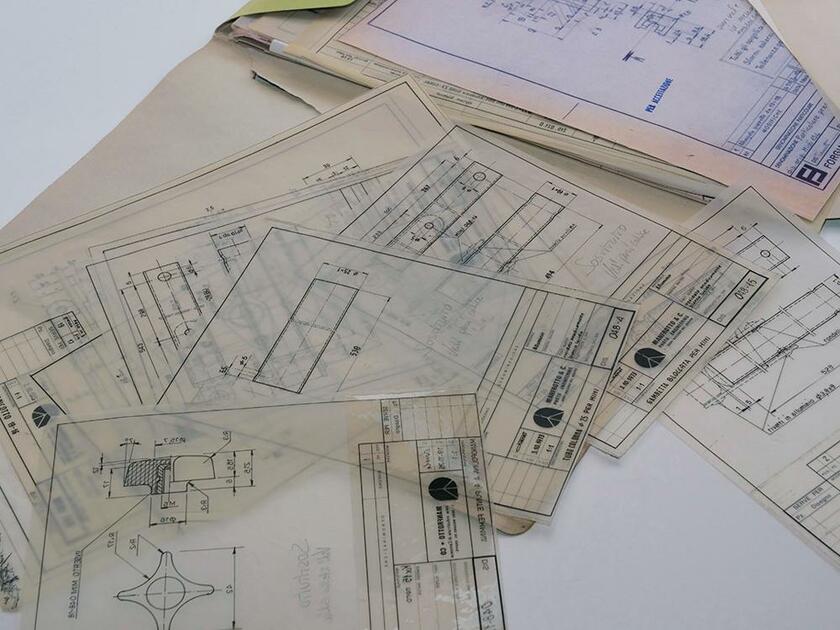
■機械化/自動化と効率よい作業
フェルトレの工場は3万平方メートルの敷地にF1~7までの七つの棟がある。F3は事務/食堂棟だが、それ以外は工場施設だ。多くの自動化された機械がならぶ。三脚の生産では、部品の製造はかなりの部分で機械による自動化が図られていた。パイプの切断や塗装は基本的に機械が担う。前述の近隣の工場で作られたモールド成型による部品は、余計な部分も残った状態で納入される。ここから余計な部分を削って奇麗にしていく。形状や数によって機械化・自動化されている部品もあれば、手作業のものもある。
バリなどが取られたパーツは塗装に回される。その際、部品をつるしておくラックには番号が書かれており、どんな塗装をするかわかるようになっている。塗装の工程では、天井のレールによってラックごと運ばれ、塗装/焼き付けされていく。複雑な形状の部品では、スプレーガンによる手作業をしているものもあったが、基本的に機械が自動で塗装していた。また有害な物質は使ってないようで、見学の際マスクなどは不要だった。
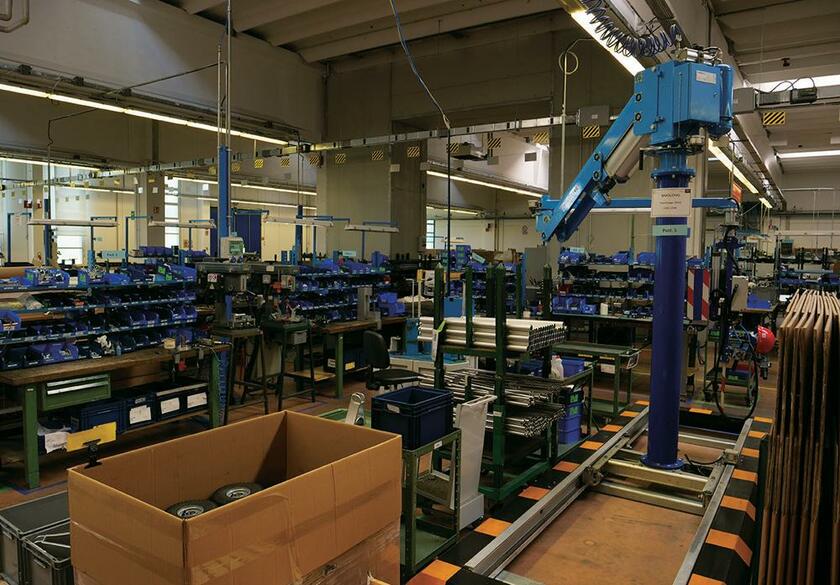
そうして作られた部品が集められ最終的に組み立てられる。組み立てはセル生産で行われる。コの字形に配置されたテーブルで、数人で作業を分担して組み立て、箱詰めまで済ませる。
その際、なぜそう組み立てるのか設計者が工員に説明しているという。その作業の必要性を理解してもらうことで、確実性と効率を向上させる。また一つの作業を繰り返させるのではなく、複数の製品の製造に携われるように一人がいろいろなスキルを持つようにしていた。こうした施策が、従業員の定着率の高さにつながっているのだろう。
■KAIZENとKanban方式
工場で目につくのが赤いシャツを着たグループの存在。背中に白く書かれた「KAIZEN」の文字が飛び込んでくる。ヴァイテックの工場でもトヨタの「改善」方式が導入されているのだ。現場の作業員とKAIZENチームの共同で、ここはこうしたほうが動きは少なくなるのでは?作業の順番を変えたら? 資材や作業台の配置の検討、破棄を減らすなども含め、生産効率を上げる改善が行われている。現場の作業員だけでなく、KAIZENチームがいるのは言い出しっぺが損をしないようにするためだそうだ。もちろん、やってみてダメだったら元に戻す。改善結果によっては、表彰する仕組みも用意されているという。新しい製品の生産も初めはKAIZENチームによって手順が検討されるそうだ。